The ultimate method to effectively clean your woven and non-woven tooling.
The process you use to clean your tooling is a critical factor that directly effects the efficiency of your business. Ultrasonically cleaning your spinnerettes, breaker plates and extrusion tooling is fast, reliable and 100% effective. Also, Ultrasonic cleaning eliminates the danger of using and disposing of hazardous solvents or fluidized salt baths.
how does ultrasonic work
Ultrasonic cleaning is the rapid and complete removal of contaminants from objects by immersing them in a tank of liquid flooded with high frequency sounds waves. These non-audible sound waves create a scrubbing brush action within the fluid.
The process is brought about by high frequency electrical energy that is converted by a transducer into high frequency sound waves – ultrasonic energy. Its ability to clean even the most tenacious substances from items derives from the core of the unit: the transducer. The cleaning power of a unit stems from the transducers performance.
The efficiency of the transducer will affect both the cleaning time and efficacy achieved during the cleaning cycle. A poor quality transducer will use more power and take longer to clean items than a good transducer. This is why TRANSONIC have invested in this area in such great depth, in order to provide you with a benchmark transducer.
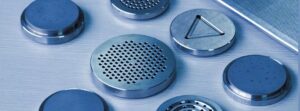
The ultrasonic energy enters the liquid within the tank and causes the rapid formation and collapse of minute bubbles: a phenomenon known as cavitation. The bubbles rapidly increase in size until they implode against the surface of the item
immersed in the tank in an enormous energy release, which lifts contamination off the surface and innermost recesses of intricately shaped parts.
It is this ability to clean box joints, hinges and threads quickly and effectively that has made ultrasonic cleaners the first choice for many industries for over 25 years.
There are many variables which need taking into account when cleaning items. Heat, power, frequency, detergent type and time all affect the cleaning process but the flexibility of ultrasonic means that these can all incorporated into the process in order to achieve the most effective results.
This photograph (right) shows Ultrasonic cleaning in action on a pair of surgical forceps. The bubbles can be clearly seen forming around the item.
As the bubbles implode and cavitation occurs, the cleaning solution rushes into the gap left by the bubble. As this fluid makes contact with the forceps, any contaminants that are present are removed.
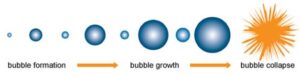
The differece of ultrasonic generators
Sweep-frequency generator has long been known in many fields such as measuring the responses of filters, amplifiers and electrical components via a variety of frequency bands. Sweep-frequency generator circuit had been widely applied in ultrasonic cleaning industry since 90's. Generators are designed to sent the signal which can be varied slightly in a range of frequencies to cleaning transducers. It plays a major role in improving the cleaning effect and prevent from damage to some vulnerable pats by single frequency ultrasonic energy.
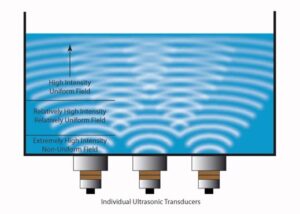
Principle of sweep-frequency technology
In general cleaning system, ultrasonic transducers are mounted on the bottom of the stainless steel tank to operate effectively at a certain frequency. Through utilizing sweep-frequency generators, a sinusoidal signal is automatically swept between two frequencies which are determined by the circuitry. The output can be applied to transducers at constantly changing frequencies. Each transducer can be drived at a very narrow frequency band. That means the frequency circuit sweeps the output frequencies to transducers between a bandwidth slightly higher and slightly lower than their resonant frequencies. If a transducer is excited by a frequency which is not closed to its frequency band, the power will drop sharply and the transducer may be damaged by tremendous heat. So that most of sweep-frequency circuits are designed different by only 2-3kHz to natural frequency, to make sure that powerful cavitation energy is released at the sweeping frequency range.
Waveform design for sweep-frequency circuit
1) Design of random sweep rate
The traditional sweeping mode, that is to say: sweeping at a single rate, is not considered as a an efficient design for cleaning work. When a oscillator is swept through a range of frequencies, obviously the output energy is not equal at different frequencies. Commonly, the output energy can reach maximal value around the center of bandwidth. So that the parts to be cleaned will be excited into resonance twice during a period of sweeping cycle.
The waveform with random sweep rate can change the spacing between the power pulses. Based on this, the pulses are emitted into the fluid at non-constant frequency, there is no single frequency repeated over and over to excite the parts into resonance.
2) Directional sweep from high frequency to low frequency
Compare to traditional sweeping frequency pattern, another variation on waveform is monotonic sweeping direction from high frequency to low frequency. The benefit is that an ultrasound wave with increasing expanding wavelength can be produced in the liquid, and exerts an additional upward force on contamination attached to the parts. This type of sound waves travelling from the bottom transducers to liquid level can significantly improve the cleaning effect.
Benefits of sweep-frequency generator in ultrasonic cleaning
We have already known that sweeping frequency mode means a slight constant variation around the resonant frequency. On the contrary, if an ultrasonic cleaner runs at a fixed frequency, it will cause three potential issues including stand wave, damage to parts and poor cleaning result.
1) Eliminates the standing waves
Due to the specific frequency of vibration, the reflected sound waves from liquid level may form the standing waves. Such patterns cause the unequal power intensity and lead to zebra stripes on parts to be cleaned. Even worse, some fabricated parts may be damaged by high ultrasound intensity in the areas of enhancement.
Sweep frequency circuits are designed to eliminate this phenomenon, varition of frequency distributes the high intensity effect more evenly throughout the liquid medium. The result is that standing waves are effectively broke down in the tank, and realize the ultimate goal of uniform cleaning result.
2) Minimize the damage to workpieces
As mentioned earlier, standing waves produced by fixed frequency may cause damage on some sensitive workpieces or components. Other than that, many delicate parts will fracture without shift in frequency:
When a sensitive part is excited at or near their resonant frequency, the large amplitude caused by the repetitive peak power pulses may break the delicate parts i.e. printed circuit boards. That's why we always tend to select an ultrasonic cleaner with sweep-frequency mode for cleaning electrical components.
Besides, hot spots are areas with a stronger ultrasonic effect(i.e. stronger cavitation effect). Apparently, the high concentration of cavitation bubbles are potentially harmful to parts being cleaned. Similarly, a simple solution is to sweep frequencies at random rate.
3) Frequency matching for transducers
As we know, the frequency of an ultrasonic transducer depends on various factors such as size, shape, assembling process, etc. That means there is no single resonant frequency for each transducer, instead of this, an ultrasonic transducer array with a distribution of center frequencies.
The use of non-sweeping circuit may happen to result in an response at resonant frequency for several transducers in array. The other transducers in array will work not very well due to the bad frequency matching, and further cause the reduction of output energy delivered from transducers. The result is an uneven ultrasonic field and cleaning effect in tank.
With the help of sweep-frequency generator, all the transducers can be excited at their center driving frequency during the sweeping cycle, and lead to a much more uniform acoustic field in the cleaning tank on condition that sweep rate is high enough. Generator circuit with sweep mode is significant for cleaning precision parts or instruments where highly uniform cleaning is essential.
DIFFERENCE BETWEEN TRADITIONAL SYSTEMS AND TRANSONIC ULTRASONIC CLEANING SYSTEM
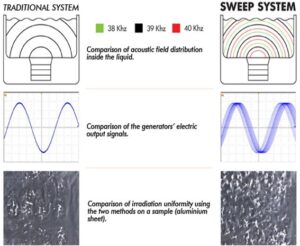